炭黑產業網據車與輪店主聯盟消息:炭黑產業網據車與輪店主聯盟消息:近日, 浙江經濟生活頻道《浙商抖抖腔》欄目發表了“我和我的工廠 走進中策橡膠”。中策橡膠集團董事長沈金榮通過該欄目為大家介紹了中策橡膠“未來工廠”。
數字化賦能,中策橡膠實現智能制造
據了解,作為浙江省首批“未來工廠”試點,杭州中策橡膠投資近5億元打造了“高性能子午胎未來工廠”。跟著鏡頭走進中策橡膠“未來工廠”,可以看到上萬個傳感器實時采集,分析生產、質量、設備等上百種數據,并自動為AGV物流機器人分派任務。
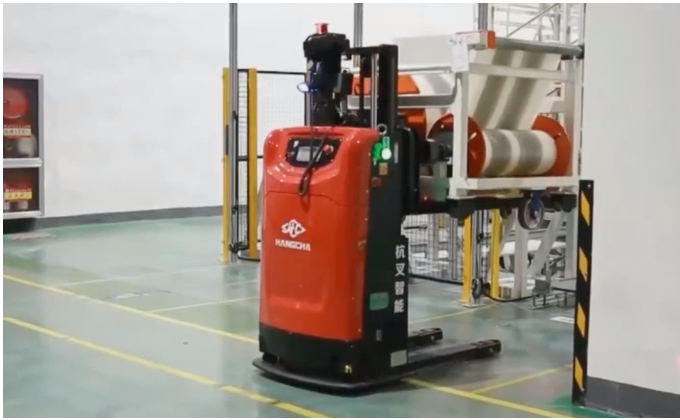
無人智能AGV叉車24小時不間斷地運行,替代人工來來回回搬運產品,提升物流效率,增加物料搬運的準確性、安全性。通過綜合應用5G、AI、大數據、云計算、物聯網等新技術,依托數字化仿真設計、大數據平臺分析決策、輪胎生產全流程智能控制與云計算模型。中策橡膠“未來工廠”成為了輪胎智能制造新模式新標桿,引領了輪胎行業制造模式轉型,加速輪胎制造產業轉化升級為智慧云制造步伐。
日產輪胎12萬條,
“未來工廠”每7秒生產1條輪胎
通過智能物流,智能智造,智能檢測等方面,中策橡膠“未來工廠”實現了全流程的智能化再造,大大提升了工廠效率,基本上6-7秒就可以生產一條輪胎。中策橡膠集團董事長沈金榮表示:“中策橡膠這幾個工廠一天加起來可以生產12萬條輪胎,這個速度在以前是沒有辦法想象的。”
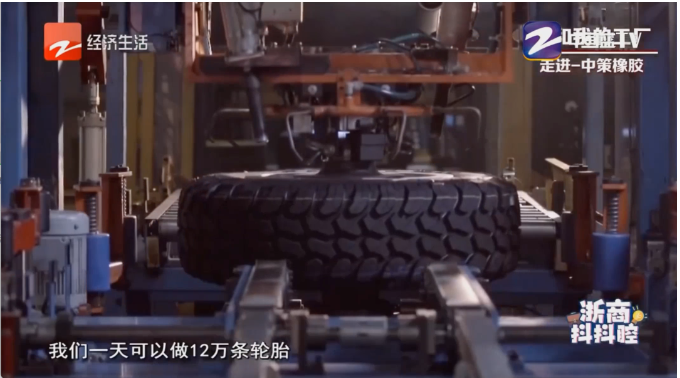
同時,生產量提升的同時,工廠所需的工人也大幅度縮減,記者在2.7萬平方米的工廠內,只看到了10個工人。
而生產效率提升、生產成本降低,可以大幅度提高了中策橡膠的市場競爭力和利潤水平。
大數據管理輪胎周期
提升產品質量和生產效率
通過MES系統的導入,中策橡膠“未來工廠”打通了輪胎生產信息流,可以全方位收集車間生產的數據信息,從而控制生產流程和工藝參數,實現了輪胎全生命周期的信息化基礎管理,從而提高企業工藝控制水平和生產效率。
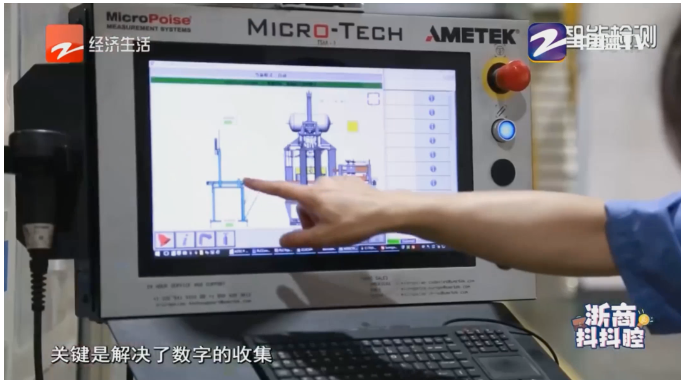
以胎面工藝為例,中策橡膠旗下有朝陽、威獅、好運、雅度等多個品牌,胎面的種類規格有上百種,產線規格每隔半小時就要切換,同時參數也需要重置。基于人工經驗頻繁重置參數,容易出現偏差。而在未來工廠里,“大腦”自動為每個規格設定更優的工藝參數,將胎面壓出產線的質量誤差控制在1%以內。數據顯示,中策未來工廠投入使用后,產品研制周期縮短50%,產品生產效率提升15%,不良率降低40%。
“低碳經濟,綠色制造”的智能工廠
中策采用全球先進的生產工藝和技術裝備,打造“低碳經濟,綠色制造”的智能工廠,將環保貫穿生產的每一環節,從生產源頭上實現廢棄物的減量化、資源化、無害化。并且中策建立再生資源循環利用體系,每產1噸再生橡膠綜合能耗降低30%,廢氣排放量減少95%以上,從而增強公司可持續發展后勁。
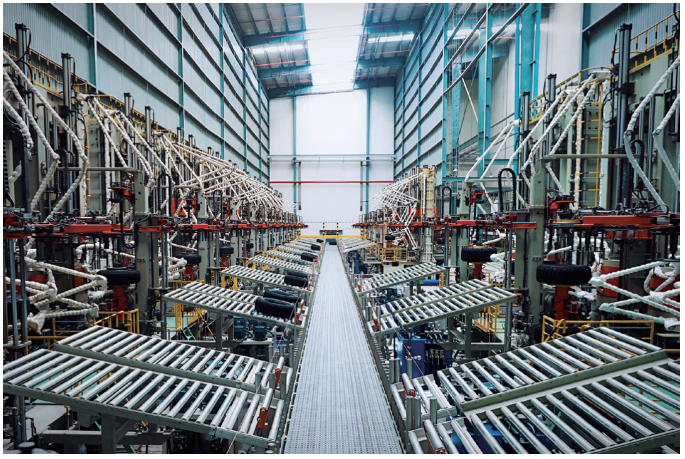
中國輪胎沒有理由輸給外資品牌近年來,隨著大數據、物聯網、云計算、人工智能、5G等技術的發展,中策橡膠積極擁抱新技術,以數字化賦能企業研、產、供、銷全產業鏈。通過數字化轉型升級,我們看到中策橡膠已經成為全球輪胎智能制造新模式新標桿,從戰略層面推動中國傳統制造業通過數字化實現轉型升級發展。我們相信,擁有全球最先進的智能工廠,加上頂尖的技術團隊和生產成本優勢,以中策橡膠為首的國產輪胎沒有理由輸于外資品牌!